Kumlama Nozulu Nedir? Nasıl Seçilir?
Kumlama nozulu, sistemin çıkış noktasında bulunan ve yüzeye püskürtülen kumun akış hızı ile yönünü kontrol eden aparata verilen isimdir. Kumlama hortumuna veya bu hortuma bağlı olarak bulunan kumlama tabancasına direkt bağlanarak sistemi tamamlamaktadır. Farklı ihtiyaçlara istinaden farklı tipte kumlama nozulları tercih edilebilmektedir. Bu yazıda kumlama nozulları ve temel özellikleri ile ilgili rehber niteliğinde detaylı bir bilgilendirme yapılacaktır. Bu rehberin kumlama nozulu seçiminde sizlere yardımcı olmasını temenni etmekteyiz.
Sistemi oluşturan diğer unsurlar gibi, kumlama işleminde nozul seçimi de hem yapılan işin maliyetini hem de yapılan yüzey işleminin etkisini optimum hale getirmek için son derece önemlidir.
Doğru nozulu seçebilmek birden fazla faktörle doğrudan ilişkilidir. Bu faktörleri daraltmak ve daha anlaşılır bir hale getirmek için aşağıdaki dört sorudan faydalanabiliriz.
1- Nasıl bir püskürtme şekli istiyoruz?
Kumlama nozulunun delik şekli püskürtme şeklini de ortaya çıkartmaktadır. İçerisinden havayı ve kumu geçiren farklı geometrik şekillere sahip nozullar, bu havanın ve kumun yönlenmesini sağlayarak yüzeye kumu dar veya geniş açıda atmaktadırlar. Temel olarak ayırmak gerekirse bu delik tiplerini üç ana başlığa bölmek mümkündür. Bunlar, düz delikli, venturi delikli ve kısıtlanmış delikli kumlama nozulları olarak sıralanabilir.

Düz delikli nozul (Şekil 1; No.1)
Bu tip nozullar dar bir püskürtme şekli ortaya çıkartmaktadır. Bu da nozulun yüzeye tutulduğunda kumu görece dar bir alana püskürtmesi anlamına gelmektedir. Bu sebeple, çoğunlukla küçük parçalı işler için daha uygun olduğu söylenebilmektedir.
Venturi delikli nozul (Şekil 1; No.2 No.3)
Venturi delikli kumlama nozulları geniş bir püskürtme şekli sağlamaktadır. Nozulu yüzeye doğrulttuğunuzda kum daha geniş bir alana etki edecektir. Venturi kumlama nozulu aynı zamanda ağızdan çıkan aşındırıcı yoğunluğunu da 100% oranında artırmaktadır. Bu nozullar daha büyük parçalar kumlanacağı zaman tercih edilmelidir.
NOT: Çift venturi kumlama nozulu ve geniş boğazlı kumlama nozulu, venturi kumlama nozulunun geliştirilmiş versiyonlarıdır.
Çift venturi delikli nozul (Şekil 1; No.4)
Seri halinde iki venturi nozulun arasında atmosferik havayı içeri alacak bir boşluk bulunan nozullara verilen isimdir. Tasarım, püskürtme şeklini genişletmek ve aynı zamanda kum yoğunluğunu da sabit tutmak için ortaya çıkarılmıştır.
Geniş Boğaz Delikli Nozul (Şekil1; No.5)
Geniş girişli ve geniş çıkışlı bir kumlama nozulu olarak nitelenebilir. Aynı ölçüde dar boğazlı bir nozulla kıyaslandıklarında üretkenliği 15% arttırmaktadırlar.
NOT: Boru içi gibi ulaşılamayacak yerler için açılı ve özel tasarımlı kumlama nozulları bulunmaktadır. Operatörlerin kumu sektirerek bu bölgelere ulaştırmaya çalışması hem zaman hem de ürün kaybına sebep olmaktadır. Dolayısıyla bu tip kumlamalar için bu nozullar tercih etmek faydalı sonuçlar doğuracaktır.
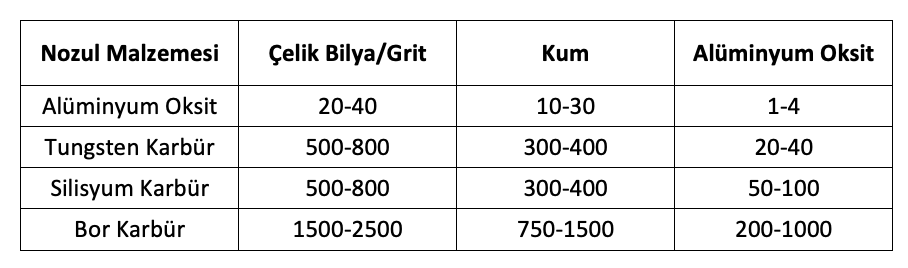
NOT: Yukarıdaki tabloda belirtilen tüm süreler tahmini değerleri göstermektedir. Püskürtme basıncına, kullanılan kumun ölçüsüne ve parçacık şekline göre bu süreler yüksek miktarda değişim gösterebilmektedir.
2- Kompresör nozulunuzu yeteri kadar besleyebiliyor mu?
Paketinden yeni çıkmış ve yüzeyinde henüz hiçbir aşınma bulunmayan bir kumlama nozulunun gerekli çalışma basıncını oluşturabilmesi için hava besleme sisteminin bu basıncın en az 50% fazlasını sağlayabilmesi gerekmektedir. Bu da yaklaşık olarak 100-140 PSI’ya tekabül etmektedir. Bu seviyelerde üretilen basınç kumlama nozulunun aşındındıktan sonra bile aynı verimle çalışabilmesine olanak sağlamaktadır.
NOT: Nozulun giriş boğazının hava besleme hortumunun iç çapıyla uyumlu olmasına dikkat edilmelidir. Aksi takdirde basınç kaybı, tabanca içi aşınma noktaları ve aşırı iç türbülans yaratmış olursunuz.
3- Kumlama nozulunun delik çapı ne olmalı?
Birim zamanda yapılan iş miktarını arttırabilmek ve en yüksek üretkenlik seviyesine çıkabilmek için ihtiyacımız olan basınca ulaşmamız gerekmektedir. Bu basınca ulaşmak için hava besleme sisteminin sunduğu basınç miktarı ve akış hızı göz önüne alınmalıdır.
Kumlama nozulunun genişliği arttıkça sağlanması gereken basınç miktarı da artacaktır. Güçsüz veya eski bir tip kompresörünüz varsa bu sürekli olarak duraksayan bir sistem ortaya çıkarabilmektedir. Dolayısıyla bu durumda daha dar delikli bir nozul seçmenizde fayda vardır. Başka bir durumda, hava besleme sistemi yüksek miktarda güç sağlayabiliyorken, sağladığı bu basıncı ortaya çıkaracak bir kumlama nozulu kullanılmazsa, potansiyel olarak sahip olduğu iş yapma gücü azaltılacak ve bu sebeple verim oldukça düşecektir.
4- Kumlama nozulu materyallerinden hangisi tercih edilmelidir?
Kumlama nozulu materyalini seçerken dikkat edilmesi gereken ana unsur seçilen kumun kendisidir. Bunun yanı sıra kumlama nozulunun kullanım süresi, işin büyüklüğü ve zorlukları göz önünde bulundurulmalıdır.
Alüminyum oksit nozul
Kullanım sürelerinin uzun olmadığı kumlama işlemleri için uygundur. Fiyatın öncelik, nozul ömrünün ikincil planda olduğu yerler için iyi bir seçenek olduğu söylenebilir.
Tungsten karbür nozul
Uzun kullanım ömürleri vardır. Mineral ve kömür cürufu kullanırken tercih edilebilir.
Silisyum karbür nozul
Tungsten karbüre çok yakın bir servis ömrü ve dayanıklılık gösterir. Avantajı ağırlık olarak tungsten karbürün üçte biri olmasıdır. Uzun süreli işlerde operatörü yormaması için bu hafif nozul tercih edilebilir.
Bor karbür nozul
Uygun hava ve aşındırıcı kullanımıyla çok uzun bir kullanım ömrü sağlamaktadır. Agresif ve sert aşındırıcılar için oldukça ideal bir nozuldur. Agresif aşındırıcılar kullanıldığında silisyum karbürden iki, üç kat, tungsten karbürden ise beş, on kat daha fazla aşınmaya direnç gösterir.
Bu sorulara verilen cevapların ortaya çıkaracağı sonuç ile doğru kumlama nozulunu seçmek mümkündür. Seçtiğimiz nozulun yaptığımız işi doğrudan etkileyerek hem maliyeti hem işin kalitesini değiştirdiğini aklımızda bulundurmamız her zaman faydalı olacaktır.